Discover our Escomatic® machines
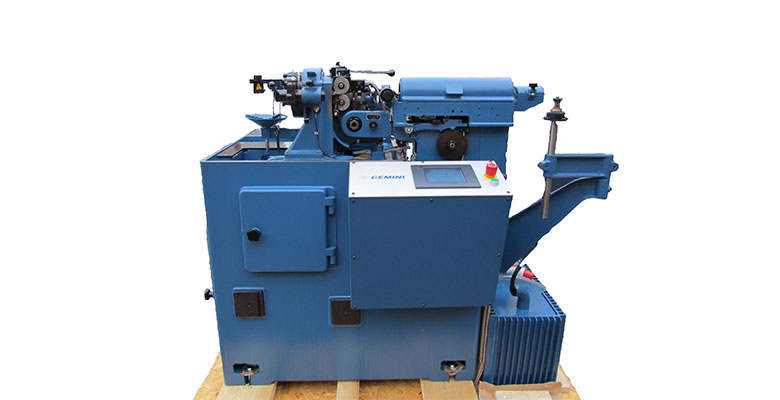
GEMINI G2-CV-74
The automatic turning lathe GEMINI G2-CV-74 can produce turned parts from coils.
The rotating headstock is a mechanical assembly of great precision and is used to do the turning and
parting off “pipe free”.
The two solide carbide constant profile tools are re-ground easily and all radial and axial adjustments are made with micrometric screws.
The counter collet attachment holds the part during part off, giving a “pipe free” component.
To facilitate access to the cutting tools, guide bush and collet, the counter collet assembly can be
lifted on one slide. It allows the use of a centring microscope to adjust very accurately the tool
positioning.
The material feed is controlled by two feed rollers. The feed rollers pressure can be adjusted to
eliminate all possible marks on the outside of the material.
The straightening device is fitted by five rotating straightening holders and carbide pads.
The CV-system is a camshaft speed variator and allows for fine turning of the feed rates. The
programming is extremely easy and adjustments can be made while the machine is running.
Productivity can be improved and very little maintenance is needed, as there is no gearbox. The gear
changes are also eliminated.
SAFETY DEVICES
They stop the machine in case of:
– Voltage drop in the power supply.
– Lack of lubricating oil in the tool head and turret.
– End of material.
– Decrease in the revolutions of the tool-holder head.
TECHNICAL DATA
– Maximum ø capacity : 5.00 mm (brass and mild steel), 4.00 mm (stainless steel).
– Maximum length in one stroke : 74.00 mm.
– 2 rotative cutting tools.
– 1 fixed counter collet
– Maximum headstock speed : 8'000 r.p.m.
– Straightener speeds : from 500 to 3'700 r.p.m
– Floor space : 1’560 x 2’000 mm.
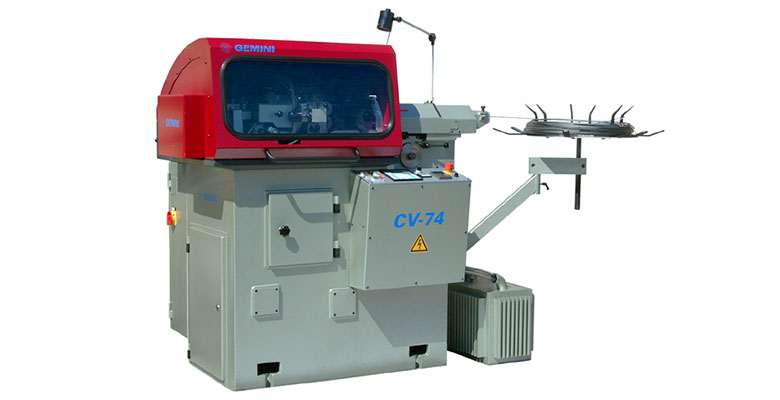
GEMINI G4-CV-74
The automatic turning lathe GEMINI G4-CV-74 can produce turned parts from coils.
The rotating headstock is a mechanical assembly of great precision and is used to do the turning and parting off “pipe free”.
The two solide carbide constant profile tools are re-ground easily and all radial and axial adjustments are made with micrometric screws.
To facilitate access to the cutting tools, guide bush and collet, the counter collet assembly can be
lifted on one slide. It allows the use of a centring microscope to adjust very accurately the tool
positioning.
The turret is equipped with three stations, including: 1 counter pliers spindle and 2 drilling spindles.
The station change is carried out in a quarter of a second by a Maltese cross mechanism. The locking
is done by a conical finger whose axis is parallel to that of the spindles but located on a larger radius.
This technique guarantees precise positioning.
Le redresseur indépendant est équipé de 4 canons rotatifs réglables et d’un canon central mobile qui, poussé au-delà de l’axe du rotor, provoque le redressage par cambrage du fil.
The CV-system is a camshaft speed variator and allows for fine turning of the feed rates. The
programming is extremely easy and adjustments can be made while the machine is running.
Productivity can be improved and very little maintenance is needed, as there is no gearbox. The gear
changes are also eliminated.
SAFETY DEVICES
They stop the machine in case of :
– Premature jamming.
– Non-recoil of the counter-collet..
– Voltage drop in the power supply..
– Lack of lubricating oil in the tool head and turret.
– End of material.
– Decrease in tool head revolutions.
TECHNICAL DATA
– Maximum ø capacity : 5.00 mm (brass and mild steel), 4.00 mm (stainless steel).
– Maximum length in one stroke : 74.00 mm
– 2 rotative cutting tools.
– 1 Turret with 3 positions
– Maximum headstock speed : 8'000 r.p.m
– Straightener speeds : from 500 to 3'700 r.p.m.
– Floor space : 1’560 x 2’000 mm.
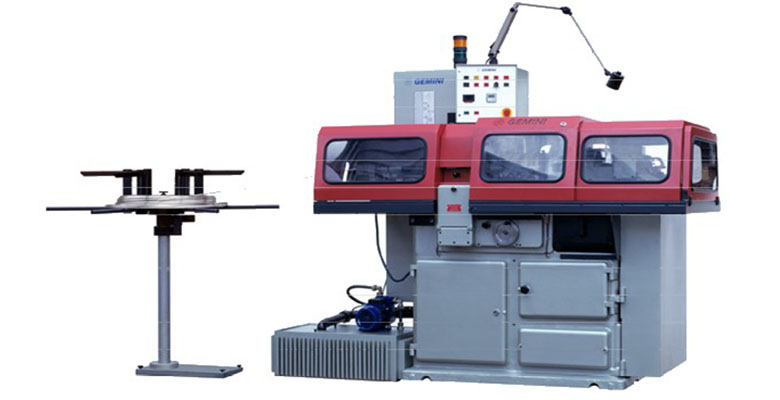
GEMINI D6SR1A
The automatic turning lathe D6 can produce turned parts from coils.
Our D6 machines are totally dismantled, repaint and fully reconditioned mechanically and electrically. All safety devices are fitted to meet CE safety standard.
The rotating headstock is a mechanical assembly of great precision and is used to do the turning and
parting off “pipe free”.
The headstock casting is fitted on a slide so the assembly can be pulled out easily to gain access to
the tools, guide bush and counter collet. In that position, the centering microscope can be used to
adjust very accurately the tools position.
The feed and holding collets are part of the headstock, together with the guide bush.
The straightening device is fitted with five rotating straightening holders and carbide pads.
Numerous attachments can be fitted to the machine to produce slots, flats, holes, threads etc… on
the front, rear or slide of the component. We can also design and manufacture special attachments
to suit particular need.
TECHNICAL DATA
– Maximum ø capacity : 9.00 mm
– Maximum length in one stroke : 62.00 mm
– 3 rotative cutting tools.
– 1 fixed counter collet our 1 Turret with 4 positions.
– Maximum headstock speed : 7'100 r.p.m
– Straightener speeds : from 500 to 3'700 r.p.m
– Floor space : 1’000 x 3’400 mm.
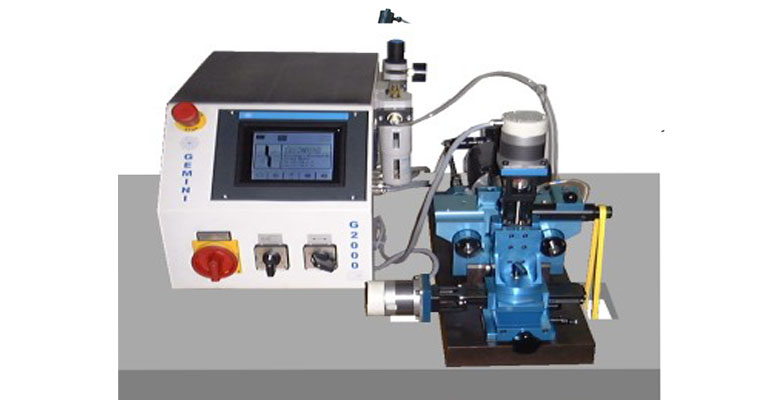
GEMINI G-2000-CN
The machine GEMINI G-2000-CN has been designed to manufacture solid carbid form tools for the
G2-CV-74, D2, G4-CV-74, D4, D5, D6, CN, Newmach and TOR-4 machines, using diamond wheels.
It is fitted with two step motors. One for the vertical movements, and one for the horizontal
movements. The cross slide is driven by a numerical control, allowing the grinding of all different
profiles.
The grinding spindle is lubricated by an air mist system.
The programming of the machine is extremely easy, and done via a touch screen. 250 profiles can be
stored in the memory or on tape.
TECHNICAL DATA
– Spindle speed : 15’000 – 30’000 r.p.m.
– Slide movement : 18-36 per minute.
– Maximum slide stroke : 18mm.
– Adjustment of the spindle : 180 degrees.
– Vertical tool holder relief adjustment : 0-6 degrees.
– Horizontal tool holder relief adjustment : 20 degrees.
– Machine size : 200x575mm.
– Bench size : 1’000 x 1’150mm.